The fourth industrial revolution or Industry 4.0 has enabled organizations to achieve good efficiency and quality by emphasizing technology that consistently optimizes processes.
Organizations need to ensure maximum quality output without having any major downtime to ensure they stay on level with the competition.
Planned maintenance and repair is crucial in optimizing the efficiency and value offered by machinery. It can prune machine downtime by over 20% and increase operational efficiency by over 10%.
Despite the benefits it offers,
performing maintenance and repairs remains a herculean task for industries owing to a shortage of trained workforce, inaccessibility of machines, and a host of other factors that compound the problem.
Fortunately, since the advent of AR, organizations can now increasingly optimize the maintenance process with relative ease.
AR takes the maintenance process to the right people, at the right time with the best technology, without having to take the technicians to the field.
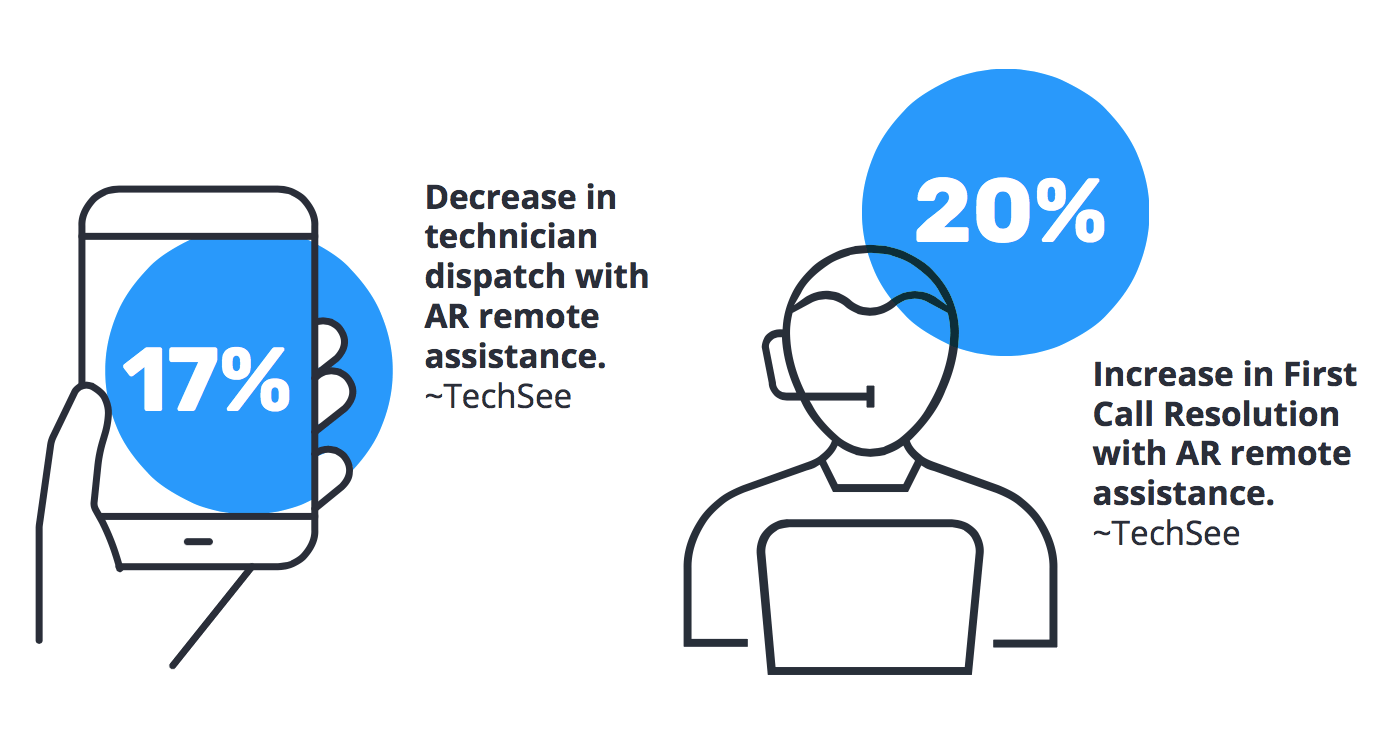
Augmented reality maintenance and repair:
From the Boeings that conquer the skies to the medical devices that microscopically examine our blood, millions of machines have derived immense benefits from undergoing maintenance aided by AR.
Here are five reasons why organizations should leverage the power of AR to derive the best outcomes from their maintenance and repair processes.
Enabling access in remote or inaccessible areas:
More often than not, heavy machinery in power plants, assembly lines, and large-scale manufacturing units are installed in remote and inaccessible areas, as installing them in urban locations is difficult.
In such scenarios, when a breakdown occurs, it is exceptionally difficult or virtually impossible to enable expert technicians to reach the location of repair within a short span of time.
Additionally, it is cumbersome to collate and store vast amounts of maintenance instructions in the form of manuals in such locations.
AR enables the organization to take the problem to the field technicians by virtually enabling them to access the machinery with the click of a button and also helps the service personnel at the site access the expertise of the personnel who aren’t physically present at the site.
It shatters geographic and linguistic boundaries and enables the machinery to be serviced within the shortest possible time.
Reinforcement of indications and troubleshooting with experienced technical support:
Experience and expertise always come at a premium price.
Most heavy machineries have thousands of components and might fail or cease to work because of one small bearing or washer.
In such a scenario, troubleshooting and pinpointing the cause of failure and solution is extremely cumbersome without the right expertise.
AR enables establishments to contact the experts,
who in turn can virtually access the machinery without having to travel to the site of breakdown and suggest solutions to resolve the problem.
Additionally,
the organizations can save on logistics costs and consult multiple experts at the same time to enable quicker problem solving.
Optimized knowledge transfer and specialized technical assistance:
Knowledge is wealth, and the expertise transferred by veteran technicians is extremely valuable. Often senior service and maintenance personnel retire even before a replacement technician is found.
In such a case,
training the junior service technician without the able guidance and input of the seniors becomes excruciatingly difficult owing to the gap in knowledge transfer.
AR can be used to create a virtual repository of sorts that can be accessed and used to train new professionals on the job.
Additionally, in the case of novel problems which do not occur frequently, technicians may have insufficient expertise.
In these cases,
AR is extremely handy, as it can be used to document the troubleshooting process to help the technician solve them when they occur and assist with efficient recall or call back.
Incident reporting for failure and efficiency analysis:
Instances of failure are frequently unreported or under-reported in the case of maintenance and repair.
Maintaining a clear record of incidents is exceptionally important to facilitate future maintenance and avoid (or prevent) catastrophic failures.
With AR, organizations and technicians can report incidents and maintain an automated record without manually having to maintain the database.
This allows them to be more organized in their decision-making and planning process.
It also helps them to raise a flag with suppliers and vendors in the event of repeated or unacceptable (majority or catastrophic) failures.
Enhancing predictive maintenance and repair:
The best way to ensure optimum planning and maintenance is to solve problems before they occur.
Predictive maintenance is key in ensuring that machinery are well maintained and does not fail at unexpected instances.
AR and IoT combine to ensure that technicians are reminded at intervals to inspect the machines for any issues. This significantly reduces downtime.
Imagine knowing the maintenance schedule weeks or months in advance and planning the production schedule in advance. AR enables that and more!
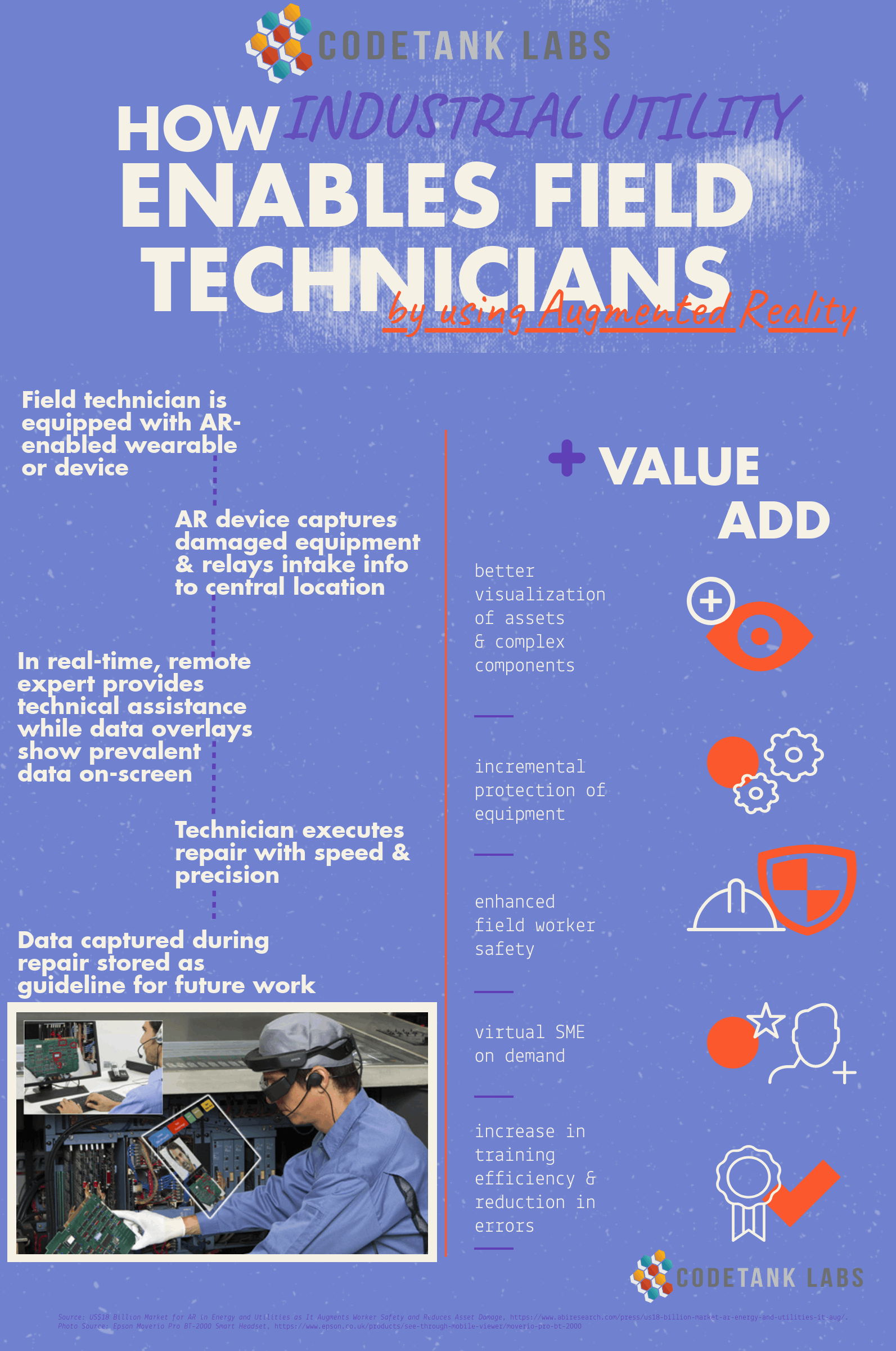
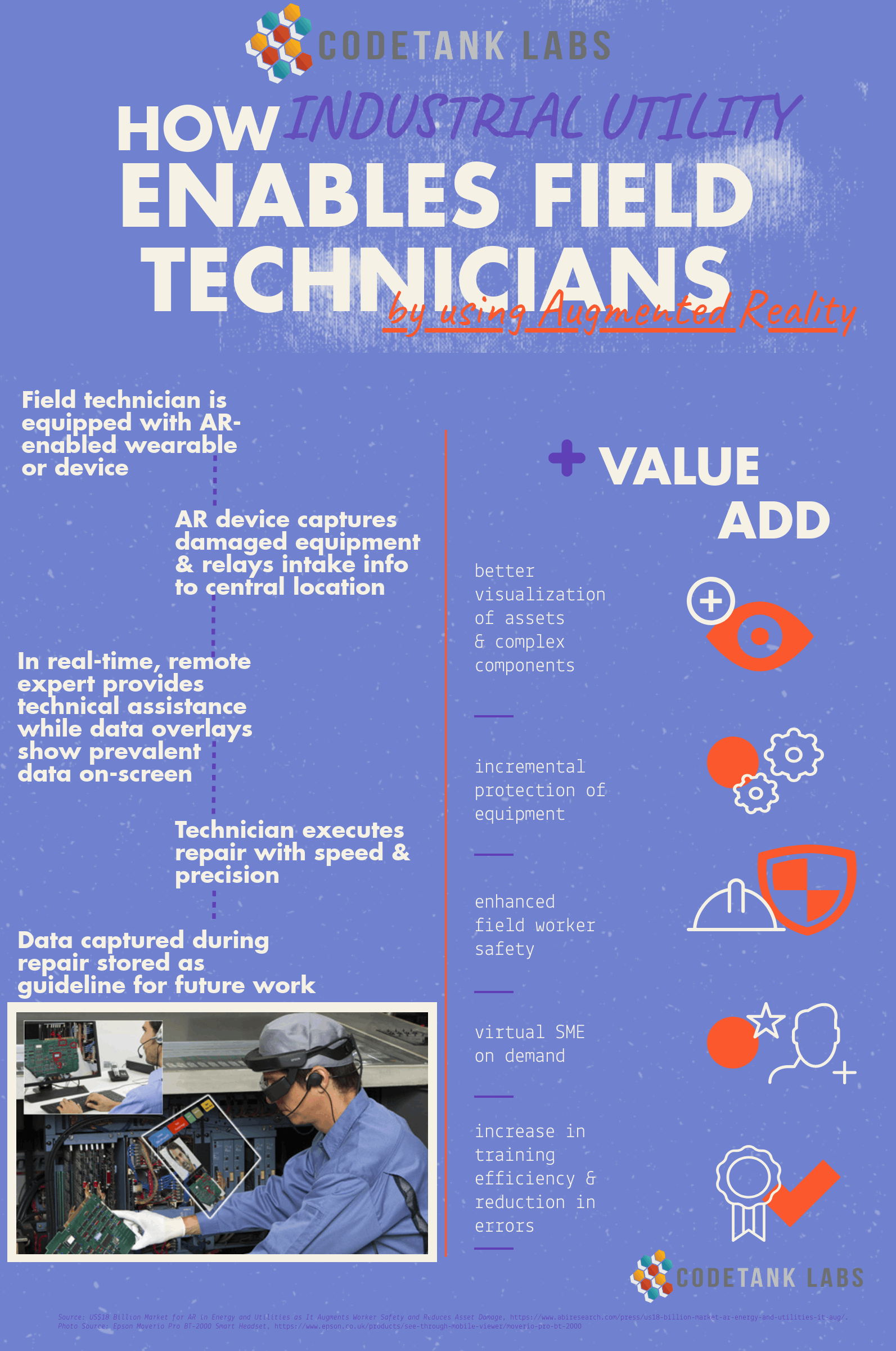
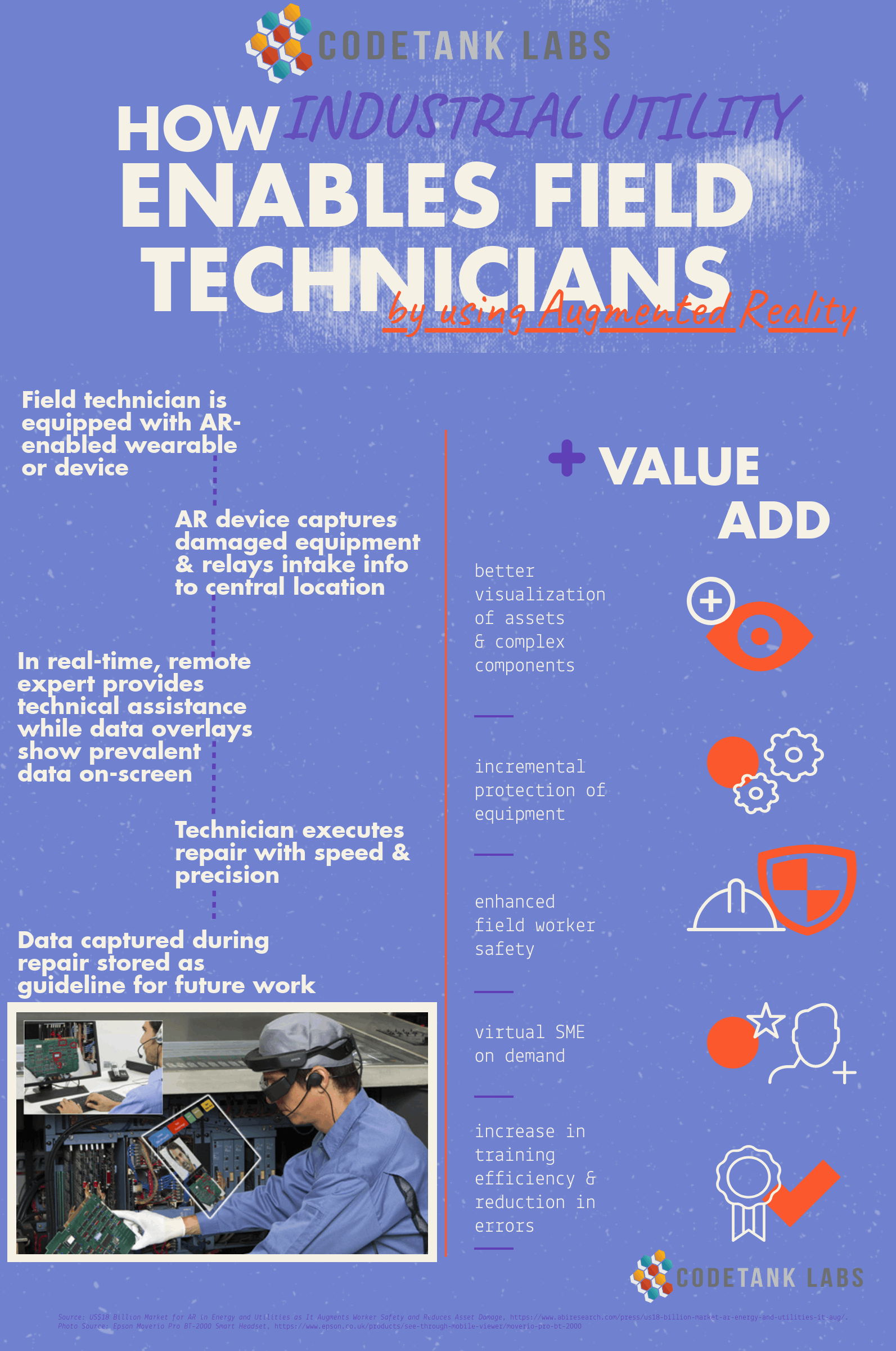
The bottom line
AR is a vital tool that can optimize the lifetime value and efficiency offered by machinery.
Organizations that employ machinery that requires frequent inspection and service derive immense benefits from getting the right expertise, timely inputs, and best service
when AR is used in conjunction with IoT and the other components of Industry 4.0.